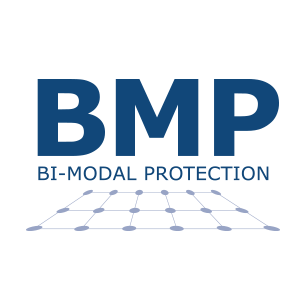
BMP®
SAFE FOR YOU,
EFFECTIVE FOR YOUR ANIMALS
BMP® Bi-Modal Protection is the Dox-al patented technology used to fix active ingredients, such as vitamins, trace elements, antibiotics and medicated premixes, to a carrier in two separate phases by means of a mixture of additives. It is not a simple microencapsulation process, but a more complex technology that uses supports and fixers selected after careful evaluations.
The characteristics of products treated using the BMP® process have gradually become the reference standard for elaborating European safety directives.
Discover the features and the impact of the bi-modal protection BMP
(Patented)

THE WINNING PREMIX
Unlike traditional premixes obtained simply by diluting the active ingredients, BMP® increases the stability of the product through the protective coating that reduces the inactivating effects of air, moisture and trace elements.
In addition, the size of the BMP® granules is adapted from time to time depending on the combination with the target food, to allow maximum mixing and thus ensure that the administration of supplements reaches all the animals and in the expected quantities.
Initially designed to limit the toxicity of some additives, it is suitable for coating any chemical agent not only to neutralize any hazardous effect it may have but also to make sure that it is not degraded or modified through contact with other substances.
BMP® ADVANTAGES
ADVANTAGES FOR THE NUTRITIONIST
Used to reach predetermined objectives in terms of guaranteed optimum intakes reducing risks for overdoses or under dosage.
ADVANTAGES FOR THE FEED
Controlled particle size, not hydrophilic or lipophilic, no static electricity: optimum characteristics for high mixing efficiency.
ADVANTAGES FOR THE OPERATOR
Safe to handle: no inhalable dusts smaller than 50 microns.
ADVANTAGES FOR THE PLANTS
Optimum flowability, no caking, it improves the stability of the premix and reduces the risk of cross-contamination.
ADVANTAGES FOR THE ANIMAL
Accurate dosing of the active ingredients and certainty of their bioavailability in time.


THE GRANULE
REVOLUTION
ox-al BMP®. Designing feed for animals
The BMP® technology was inspired by Dox-al’s desire to constantly improve its products and manufacturing processes, using research to explore new pathways.
Pathways oriented by the clarity of its objectives, which consist in improving the health of the operators as well as that of the animals.
A minor revolution with major results that Dox-al has put at everybody’s disposal.
Adapting size for easier dosing
Uniform distribution of the active ingredient depends on one property in particular: flowability. When it is low, as in powders, underdosing or overdosing may occur.
The BMP® technology enables the technological properties of micro-ingredient to be modified by increasing the size of the particles, whether the product is a raw material, premix or supplementary feed.
It also increases flowability, which improves the dosing of the products mixed.
Ensuring compatibility with the feed
The particle size of each product is designed and produced to ensure compatibility with the ingredients of the feed to which it is to be added.
The surface of the particles of a BMP® product is rough and uneven so as to adapt to the characteristics of the feed.
Making it dense like the feed
If two materials with a different specific weight and density are mixed, they readily become unmixed and separate.
This happens with powders but not with BMP® granules, because they are formulated with a density compatible with that of the feed.
Reducing the inactivating effects of light and air and lower absorption of moisture.
As a BMP® granule is larger and denser than an equivalent volume of powder, the surface area that comes into contact with the atmospheric agents is reduced and consequently the active ingredients inside are protected against processes like oxidation.
A question of stability
With BMP®, all the particles of the various active ingredients, which could spoil if they were to come into in contact with one another, are kept separate.
The BMP® granules enable the single elements to remain stable because the single particles contained in every granule are homogeneous: the contents of one granule are protected against contact with the contents of another granule.
Nothing dissolves accidentally
Every BMP® granule has a coating made up of surfactants, selected to neutralize the hydrophilic or lipophilic properties of the particles coated.
In this way, as required, the granule can be made stable both in the presence of aqueous solutions and in mixtures with oily substances.
Nothing is left suspended
BMP® granules cannot be inhaled because they do not present microparticles that can be suspended in the air (no fractions
- Risk of contact with the skin, ingestion and, above all, inhalation of significant quantities of micro-ingredients by operators;
- Actual loss of micro-ingredients from the feed, with consequent economic damage for the manufacturer and functional damage for the animal.
Skin friends
Due to their structure and aggregation, the BMP® granules do not emit any dust into the air.
This is why the surface area of the skin that could come into contact with a particle is smaller than that of an equivalent volume of powder.
Resisting the attraction
During distribution of the feed, the various parts of the installations (screw conveyors and mixers) may generate electrical charges that create attraction and a non-uniform distribution. The BMP® granules, which are larger and have a higher specific weight than powder, reduce this considerably.
Reducing waste
BMP® granules are also effective from the point of view of using all of the product.
In fact, the granules mix uniformly and do not disintegrate so they do not create dust.
They are also resistant to static electricity and have a lipophilic and hydrophilic coating.
Due to these characteristics, products manufactured with the BMP® technology minimize the effects of cross-contamination.
Customer-tailored quality
The size of the granule is chosen according to the customer’s needs, with processes and installations developed and constructed on the basis of principles established during the company’s long-term experience.
The quality of the finished products is ensured by full control of all phases of production.
And this helps our customers to optimize their own manufacturing processes and improve their products.